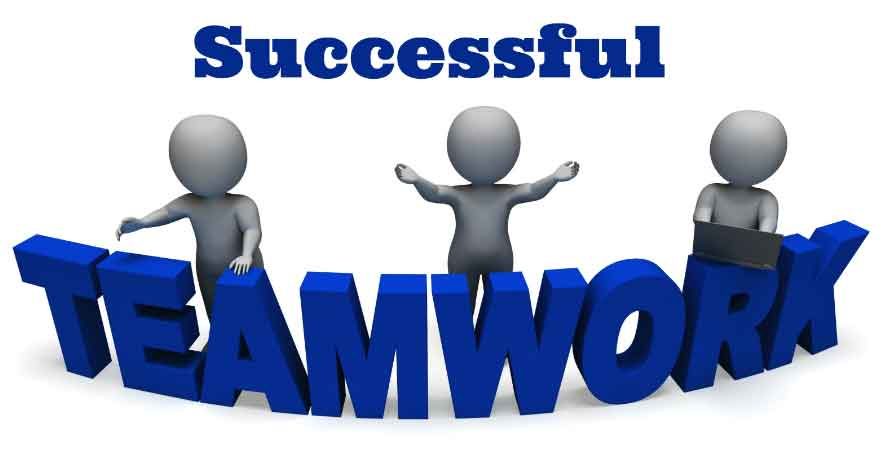
As a part of our many values here at Mohawk, practicing teamwork has always been one of the top priorities. After a recent conference with other manufacturers around the state of Delaware, a new term came into conversation when it has to do with teamwork initiatives and that is, “appropriated stress.”
To Be or Not To Be “Stressed”
The word “stress” is not a word many people associate with being positive; but, if you are not stressed on the job, is quality and set procedures being followed? The manufacturing company who brought this term up claims that when employees have an appropriate level of stress, they perform better in both quality and time efficiency. When employees are not appropriately stressed, that allows lull periods where inefficient uses of time may be present and create a more hostile work environment.
When working on a production line, if one part of the line is stressed and the other part of it has relaxed areas, in manufacturing it is time for teamwork to really shine through. If one person on the line is backed up, others who do not show the same level of stress should use lean manufacturing practices to help reduce the mounting stress from one area and making the stress load appropriate to the whole line. This in return will create an effective team work environment.
How to Implement ‘Appropriated Stress’
Whether on a manufacturing line or in an office environment, back ups, complications and other conflicts may reduce productivity. Work places often operate with a team, so if it is in the capability of other team members to help reduce the stress of others by adding some stress to their work load, it will benefit the common goal of the company. This will create a more harmonious working environment for everyone and not leave one employee to carry the weight of a team on their shoulders if others are in a position and have the knowledge and time to assist.